The E-Commerce Process: What Happens After You Click Buy?
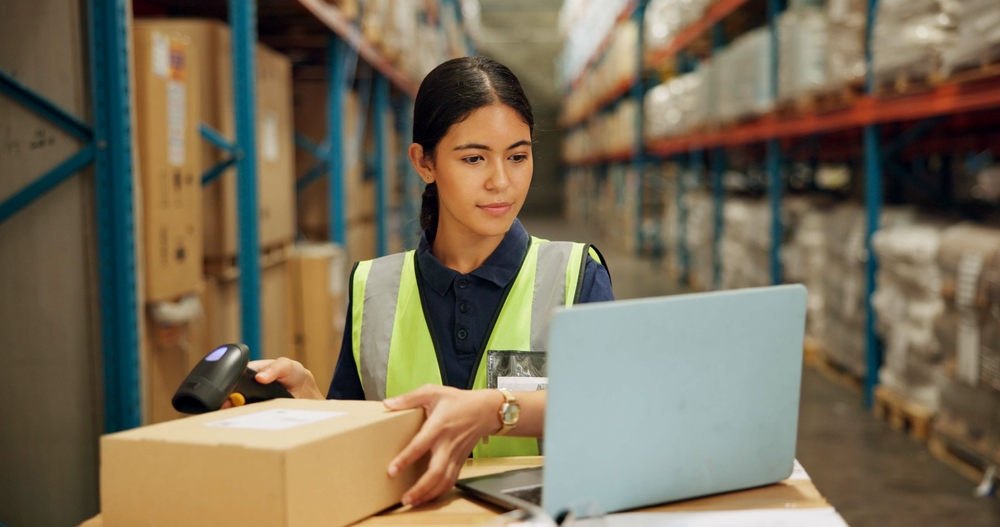
Today, purchasing online is quicker than ever before, allowing customers to complete their shopping in just one click. Due to this, it’s easy to forget that a simple online order triggers a complex process behind the scenes. It isn’t clear to many of us what happens when you click buy. We just wait for our order and pay no mind to what happens. But, there are so many people and events that happen that can help you understand the world of E-Commerce more and allow you to make thoughtful choices for your next order.
The moment you click “buy,” your order begins a logistical journey that involves sophisticated technology, skilled labor, and well-orchestrated systems designed to get your item from the warehouse shelf to your doorstep, typically within a matter of days. While the consumer experience is simple and convenient, the processes that support it are anything but.
Understanding what happens after you place an online order sheds light on the lesser-known parts of commerce, which is a fascinating process that can make you become a savvier shopper and more compassionate the next time a parcel is delayed!
Order Processing Begins Immediately
When you click buy, your order gets sent straight to the company and appears on their system. This will then be confirmed by the company, but usually these days, the order is confirmed instantly for many industries. Once your order has been confirmed, the company’s system sends it to a central order management platform. The purpose of this platform is to communicate with inventory databases to check whether the product is in stock and where it is located. If a specific product is available in multiple distribution centers, the system will determine the best location for your order to fulfill it as soon as possible. The system will base this on factors such as proximity, inventory levels, and shipping speed.
For the majority of your orders, this process will be done in a matter of seconds. This is because many companies aim to get the order into the fulfilment queue as quickly as they can to reduce the number of delays and keep customers happy. Plus, most are very busy with orders, so they need to keep on top of them; otherwise, their system will be overloaded, and workers will be in the midst of chaos.
Finding Your Order
From this, the picking stage begins. Fulfillment centers are highly organized environments that rely on a mix of human workers and automated machinery to move items quickly and accurately. Workers receive digital instructions that guide them to pick items from shelves, bins, or racks. The warehouse staff, or even automated systems, will use these to locate your product within the storage facility. However, this isn’t typically done one-by-one as each order comes through, because this would take up a lot of time. They will usually find and collect products together, known as batch picking. Workers will collect multiple orders at once to save time.
As well as this, your order will be picked in zones, which is where people are assigned to specific storage areas to make it more efficient. So, if you have multiple items in your order, depending on where they are located, different people will pick different products. This is why sometimes your parcel can arrive in a couple of separate packages, as they may be from different areas in the storage facility, or even in different distribution centers.
This may seem confusing, but don’t worry, every item is scanned and verified to ensure that it matches the order details to get it to you correctly.
Packaging Smartly
Once your order has been picked, it will move to a packing station, where it is carefully prepared for shipping. It is a thoughtful process that takes care of your items, especially for fragile products. There is a process for each type of product to ensure that your order arrives safely and intact. This may sound like a long process, but companies are more prepared to handle and package various items with care at speed. They will use the right packaging material to prevent damage and keep packaging very minimal but still secure to help reduce material costs. On top of this, materials are now more sustainable to help protect the planet and meet sustainable initiatives. The package is then labeled, sorted, and prepared for handoff to the carrier.
Shipping to Bring It All Home
With your package ready, the next phase is shipping. This involves the process of sorting orders based on destination and assigning them to the appropriate courier or delivery service. Most of the time, logistics providers like FedEx, UPS, DHL, or national postal services pick up shipments from fulfillment centers and transport them to local hubs. However, sometimes, depending on where in the world you’ve ordered from and where you are, these will be transported to airports or ports, or even train stations, to be shipped worldwide by air, boat, and train. When this happens, it will be shipped across the world either by one of these methods or using multiple methods to save money and be more eco-friendly. This means the delivery can be a little longer if your products are traveling so far to reach you.
Whichever way your order travels to your home, every shipping provider will send out tracking updates so that you can stay updated on your order’s journey and know a timeline for when to expect the parcel.
The Last Stretch of Delivery
From there, items are routed to regional facilities and assigned for final delivery, often known as the “last mile.”
The last mile is one of the most expensive and complicated stages of the process. It is when your parcel leaves the final distribution center and is delivered to your doorstep which is where it faces many issues. Traffic patterns, weather conditions, and delivery volume all affect efficiency. To meet consumer expectations for speed, companies invest in route optimization software, GPS tracking, and even alternative delivery models like lockers or same-day bike couriers in urban areas. The people behind this stage work tirelessly to get your package to you on time and in perfect condition.
The Silent Infrastructure That Makes It All Possible
Behind every package that lands on your doorstep lies a world of infrastructure that the average consumer rarely sees. From barcode scanners and AI-based inventory management to temperature-controled storage and global tracking systems, the e-commerce world never stops turning.
Even the materials used in storage and transport have evolved to meet the demands of modern commerce. Durable and reusable options like plastic pallets help streamline the safe and efficient movement of goods through fulfillment centers. These play a critical role in reducing waste, protecting products, and keeping the supply chain flowing smoothly.
Clicking “buy” may seem like the end of a decision, but it’s actually the beginning of an impressive and quick process that involve many people and lots of advanced technology. As online shopping continues to grow in popularity, so does the need for faster, smarter, and more sustainable logistics. Every stage of the e-commerce process is tailored to meet the expectations of customers and fulfill them. So, next time you order, consider the hard work and effort put into getting your parcel to your doorstep quickly and in perfect condition.