Sheet Metal Welding Techniques
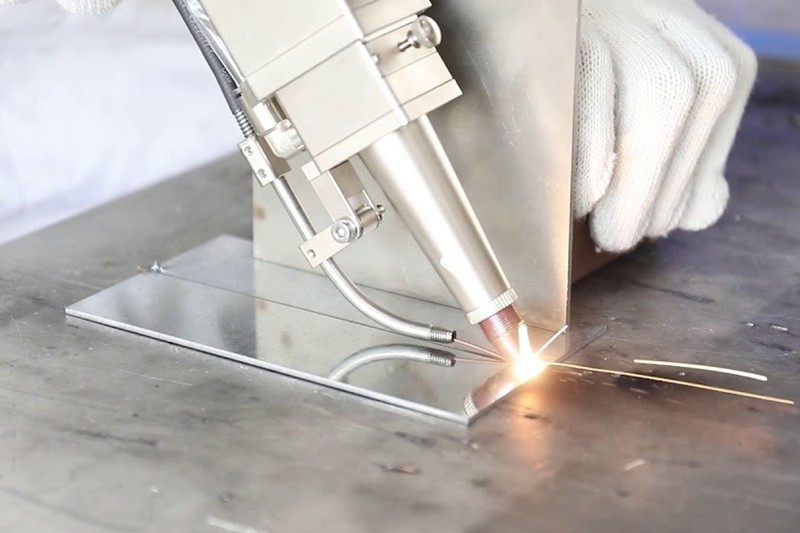
Sheet metal welding is a crucial process in various industries, from automotive manufacturing to construction. It involves joining thin metal sheets together to create strong and durable structures.
Sheet metal welding is the process of joining thin metal sheets together using various techniques and methods. It plays a vital role in creating a wide range of products, from car bodies to household appliances. Understanding welding techniques is essential for anyone involved in sheet metal fabrication.
What is Sheet Metal Welding?
Sheet metal welding is a process that involves welding thin metal sheets together under high temperatures. The welding process involves heating the workpieces to their melting point or beyond till they fuse together, forming a solid continuous bond.
Sheet metal welders work in various world industries, including aerospace, automotive, marine, electronics, assembly plants, etc. Like other manufacturing processes, making high-quality welds requires skill and expertise.
Types of Sheet Metal
There are several types of sheet metal, and choosing the right one for your project is crucial. Common types include stainless steel, aluminum, and carbon steel. Each type has its advantages and disadvantages, so selecting the appropriate material is essential for a successful weld.
Welding Equipment and Safety
Safety should always be a top priority when welding. Proper safety gear, including welding helmets, gloves, and flame-resistant clothing, is essential. Additionally, you’ll need welding equipment such as welding machines, electrodes, and shielding gas.
Common Welding Methods
Arc Welding
Arc welding is a widely used method that uses an electric arc to melt the metal and create a strong bond. It’s versatile and suitable for various sheet metal thicknesses.
MIG Welding
MIG (Metal Inert Gas) welding is known for its ease of use and high productivity. It’s an ideal choice for welding thin sheet metal.
TIG Welding
TIG (Tungsten Inert Gas) welding offers precise control and produces high-quality welds. It’s commonly used for welding aluminum and stainless steel.
Spot Welding
Spot welding involves joining metal sheets by applying pressure and heat to specific points. It’s commonly used in the automotive industry.
Preparing Your Workspace
Before you start welding, ensure your workspace is clean, well-ventilated, and free from flammable materials. Proper organization and setup are essential for a smooth welding process.
Cleaning and Surface Preparation
Cleanliness is crucial for successful welding. Remove any rust, paint, or contaminants from the metal surface using appropriate methods such as grinding or chemical cleaning.
Choosing the Right Filler Material
Selecting the correct filler material ensures a strong weld. The choice depends on the type of sheet metal and the welding method you’re using.
Setting the Welding Parameters
Adjusting the welding machine’s settings, including voltage, amperage, and wire speed, is critical for achieving the desired weld quality.
Welding Techniques
Butt Joint Welding
Butt joint welding is used to join two metal sheets at their edges. It requires precise control to avoid gaps and achieve a smooth weld.
Lap Joint Welding
Lap joint welding involves overlapping two sheets and welding along the overlapping area. It provides strength and is commonly used in sheet metal fabrication.
T-Joint Welding
T-joint welding is used to join two sheets at right angles, forming a T shape. Proper technique is essential to prevent weak welds at the joint.
Corner Joint Welding
Corner joint welding is used when two sheets meet at a corner. It requires careful preparation to ensure a strong and consistent weld.
Quality Control
After welding, it’s essential to inspect the weld for defects and ensure it meets the required standards. This step is critical for safety and structural integrity.
Common Welding Defects and How to Avoid Them
Understanding common welding defects, such as porosity and undercutting, can help you identify and prevent them in your welds.
Post-Welding Cleanup and Finishing
Cleaning and finishing the welded area will improve its appearance and protect it from corrosion. Proper finishing techniques vary depending on the project.
Applications of Sheet Metal Welding
Sheet metal welding is used in a wide range of applications, including the automotive industry, aerospace, construction, and manufacturing. Its versatility makes it an indispensable skill in these fields.
XinCheng is a machining and prototyping manufacturer that has harnessed the power of sheet metal welding to create precision components for various industries. Their expertise in this field ensures that the products they manufacture meet the highest standards of quality and durability. Whether it’s producing intricate aerospace parts or robust components for the automotive sector, XinCheng’s commitment to excellence in sheet metal welding plays a pivotal role in their success.
Conclusion
Sheet metal welding is a valuable skill with a broad range of applications. By understanding the various welding techniques, materials, and safety precautions, you can become proficient in this field. Whether you’re a professional welder or a DIY enthusiast, mastering sheet metal welding opens up endless possibilities for creating strong and durable metal structures.